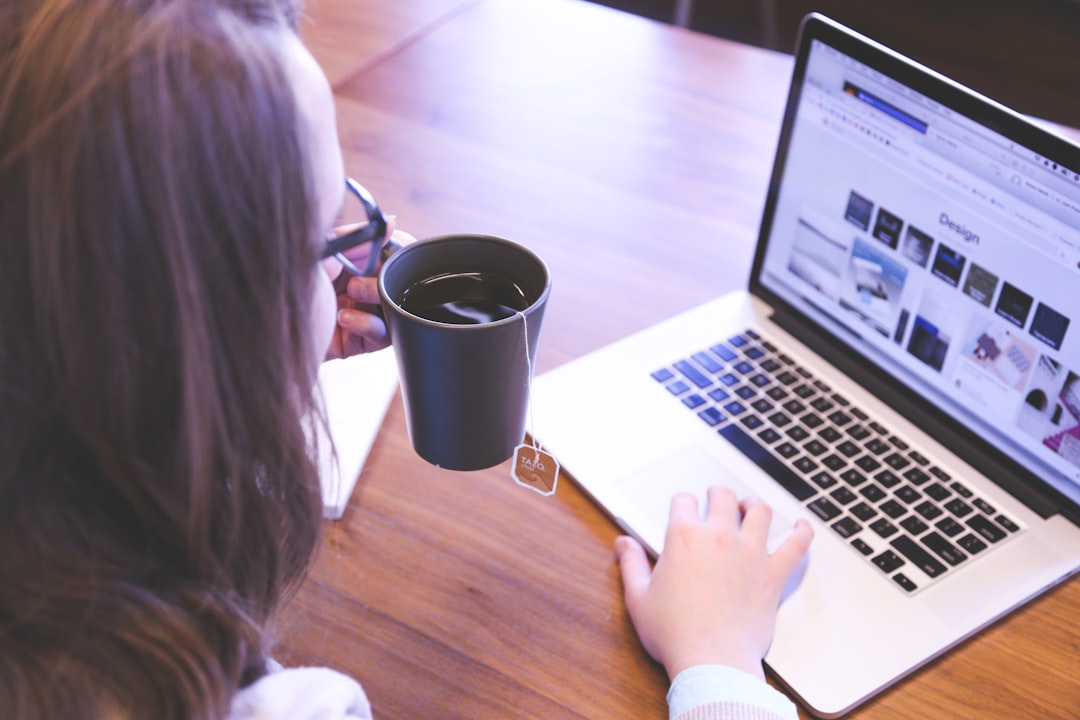
The Advantages of Industrial PCs in Modern Manufacturing
admin
- 0
The implementation of industrial automation systems has revolutionized the manufacturing and production processes by significantly increasing efficiency and productivity. With the use of automated machinery and robotics, tasks that were once time-consuming and labor-intensive can now be completed in a fraction of the time, allowing for higher output and faster turnaround times. This increased efficiency has also led to a reduction in human error, as automated systems are programmed to perform tasks with precision and accuracy, resulting in higher quality products and reduced waste.
Furthermore, industrial automation has enabled companies to streamline their operations by automating repetitive tasks, freeing up human workers to focus on more complex and strategic activities. This has not only increased overall productivity but has also improved employee satisfaction by allowing them to engage in more meaningful and challenging work. In addition, the use of automation has also led to a reduction in labor costs, as fewer workers are needed to operate and monitor the automated systems, resulting in significant cost savings for businesses.
Overall, the increased efficiency and productivity brought about by industrial automation have allowed companies to stay competitive in the global market by producing higher quality products at a faster pace while reducing operational costs.
Key Takeaways
- Implementing automation systems can lead to increased efficiency and productivity in various processes within an organization.
- Real-time monitoring and control capabilities allow for better oversight and management of operations, leading to improved decision-making and problem-solving.
- Integration with other systems such as ERP and CRM can streamline processes and improve overall business operations.
- Automation systems often come with enhanced reliability and durability, reducing the risk of errors and downtime.
- The flexibility and customization options of automation systems allow for tailored solutions to meet specific business needs and requirements.
- Improved data collection and analysis capabilities enable better insights and informed decision-making for continuous improvement.
- Automation systems can lead to cost savings and a positive return on investment through improved efficiency, reduced errors, and optimized resource utilization.
Real-time Monitoring and Control
One of the key benefits of industrial automation is the ability to monitor and control manufacturing processes in real-time. Through the use of sensors and advanced control systems, companies can gather data on various aspects of their production processes, such as temperature, pressure, and speed, and make real-time adjustments to optimize performance. This real-time monitoring and control not only ensures that production runs smoothly but also allows for quick identification and resolution of any issues that may arise, minimizing downtime and maximizing output.
Moreover, real-time monitoring and control enable companies to make data-driven decisions to improve their processes and overall efficiency. By analyzing the data collected from automated systems, companies can identify areas for improvement and implement changes to optimize their operations. This proactive approach to monitoring and control allows companies to stay ahead of potential problems and continuously improve their processes, leading to increased productivity and reduced waste.
In addition, real-time monitoring and control also provide companies with greater visibility into their operations, allowing them to track performance metrics and identify trends over time. This valuable insight enables companies to make informed decisions about resource allocation, production scheduling, and equipment maintenance, ultimately leading to more efficient and cost-effective operations.
Integration with Other Systems
Industrial automation systems are designed to seamlessly integrate with other systems within a manufacturing or production environment, providing a holistic approach to process optimization. By integrating with enterprise resource planning (ERP) systems, inventory management systems, and supply chain management systems, companies can achieve greater visibility and control over their entire operations, from raw material procurement to product delivery.
Furthermore, integration with other systems allows for the automation of data exchange and communication between different departments and functions within an organization. This streamlined flow of information not only reduces the risk of errors but also enables real-time decision-making based on accurate and up-to-date data. For example, by integrating automated production systems with inventory management systems, companies can automatically adjust production schedules based on inventory levels, ensuring that they meet customer demand without overstocking or understocking.
Moreover, integration with other systems also enables companies to leverage advanced technologies such as artificial intelligence and machine learning to further optimize their operations. By combining data from various systems, companies can gain valuable insights into their processes and make predictive analyses to anticipate future trends and demands. This level of integration allows companies to stay agile and responsive in a rapidly changing market, ultimately leading to increased efficiency and competitiveness.
Enhanced Reliability and Durability
Metrics | Values |
---|---|
Mean Time Between Failures (MTBF) | 500,000 hours |
Failure Rate | 0.1% per year |
Reliability Testing | 99.9% success rate |
Durability Testing | 100,000 cycles |
Industrial automation systems are designed to operate continuously under demanding conditions, providing enhanced reliability and durability compared to manual processes. Automated machinery and robotics are built to withstand harsh environments, high temperatures, heavy loads, and repetitive tasks without experiencing fatigue or errors. This level of reliability ensures consistent performance and minimizes the risk of unplanned downtime, allowing for uninterrupted production and higher output.
Furthermore, the use of industrial automation reduces the reliance on human labor for repetitive and physically demanding tasks, which can lead to injuries or accidents. By automating these tasks, companies can create a safer working environment for their employees while ensuring consistent quality and output. This not only improves employee morale but also reduces the risk of costly workplace incidents that can disrupt operations.
In addition, the durability of industrial automation systems ensures a longer lifespan for equipment and machinery, reducing the need for frequent maintenance and replacement. This results in lower maintenance costs and longer equipment uptime, ultimately leading to cost savings for businesses. Overall, the enhanced reliability and durability of industrial automation systems contribute to a more stable and efficient production environment.
Flexibility and Customization
Industrial automation systems offer a high degree of flexibility and customization, allowing companies to adapt their processes to changing market demands and customer requirements. Automated machinery and robotics can be programmed to perform a wide range of tasks with varying degrees of complexity, from simple assembly operations to intricate precision machining. This flexibility enables companies to quickly reconfigure their production lines to accommodate new products or changes in design specifications without significant downtime or retooling costs.
Moreover, industrial automation allows for greater customization of products to meet specific customer needs. By leveraging advanced control systems and robotics, companies can produce highly customized products with minimal manual intervention, reducing lead times and production costs. This level of customization not only enhances customer satisfaction but also provides companies with a competitive edge in the market by offering unique solutions tailored to individual requirements.
Furthermore, the flexibility of industrial automation systems extends beyond production processes to include supply chain management and logistics. Automated material handling systems can adapt to changes in demand and optimize inventory levels, ensuring that companies can respond quickly to fluctuations in market conditions. This level of flexibility enables companies to stay agile and responsive in a dynamic business environment while maintaining high levels of efficiency.
Improved Data Collection and Analysis
Industrial automation systems enable companies to collect vast amounts of data on various aspects of their operations, providing valuable insights into performance metrics, equipment utilization, and product quality. By leveraging advanced sensors and control systems, companies can gather real-time data on key parameters such as temperature, pressure, speed, and energy consumption, allowing for comprehensive analysis of their processes.
This wealth of data enables companies to identify trends, patterns, and correlations that may not be apparent through manual observation alone. By using advanced analytics tools, companies can gain a deeper understanding of their operations and make informed decisions to optimize performance. For example, by analyzing production data, companies can identify bottlenecks in their processes and implement changes to improve throughput and reduce cycle times.
Moreover, the use of industrial automation allows for predictive maintenance based on data analysis, enabling companies to anticipate equipment failures before they occur. By monitoring equipment performance metrics in real-time, companies can detect early signs of wear or malfunction and schedule maintenance proactively to avoid unplanned downtime. This proactive approach not only extends the lifespan of equipment but also reduces maintenance costs by preventing costly repairs.
Overall, improved data collection and analysis through industrial automation provide companies with valuable insights into their operations, enabling them to make data-driven decisions that lead to increased efficiency and cost savings.
Cost Savings and Return on Investment
The implementation of industrial automation systems offers significant cost savings for businesses through increased efficiency, reduced labor costs, lower maintenance expenses, and minimized waste. By automating repetitive tasks and streamlining production processes, companies can achieve higher output with fewer resources, leading to lower operational costs per unit produced. This increased efficiency also results in reduced energy consumption and lower overhead expenses, contributing to overall cost savings for businesses.
Furthermore, industrial automation reduces the reliance on manual labor for routine tasks, leading to lower labor costs for businesses. By automating these tasks through robotics and automated machinery, companies can reallocate human resources to more strategic activities while reducing the need for additional labor during peak production periods. This not only reduces labor expenses but also improves employee satisfaction by allowing them to engage in more meaningful work.
In addition, the enhanced reliability and durability of industrial automation systems result in lower maintenance costs for businesses. Automated machinery is designed to operate continuously under demanding conditions without experiencing fatigue or errors, reducing the need for frequent repairs or replacements. This leads to longer equipment uptime and lower maintenance expenses over time.
Moreover, industrial automation minimizes waste through precise control over production processes, resulting in lower material usage and reduced scrap rates. By optimizing production parameters through real-time monitoring and control, companies can minimize overproduction and ensure consistent quality while reducing waste disposal costs.
Overall, the cost savings achieved through industrial automation contribute to a significant return on investment for businesses by improving operational efficiency and reducing overall production costs.
Industrial automation helps businesses streamline their processes, increase productivity, and reduce the need for manual labor. This not only leads to cost savings in terms of labor expenses, but also minimizes the risk of human error and increases the speed and accuracy of production. Additionally, automation can optimize resource utilization and reduce waste, further driving down production costs. As a result, businesses can achieve a significant return on investment through industrial automation, ultimately improving their competitiveness and profitability in the market.
If you’re interested in learning more about industrial PCs, you should check out this article on Tech Blog Hunting. They have a great piece on the latest advancements in industrial PC technology and how it’s revolutionizing the manufacturing industry. It’s a fascinating read that delves into the various applications and benefits of using industrial PCs in different sectors. Whether you’re a tech enthusiast or a professional in the field, this article is definitely worth a read.
FAQs
What is an industrial PC?
An industrial PC is a computer designed for use in industrial environments, such as manufacturing plants, warehouses, and other harsh or rugged settings. These PCs are built to withstand extreme temperatures, humidity, dust, and vibration, and are often used for controlling machinery and equipment.
What are the key features of an industrial PC?
Key features of industrial PCs include rugged construction, fanless design for better reliability, wide operating temperature range, resistance to dust and water, and compatibility with industrial protocols and interfaces. They are also often designed for long-term availability and support.
What are the typical applications of industrial PCs?
Industrial PCs are used in a wide range of applications, including process control, machine automation, data acquisition, monitoring and control of equipment, and industrial networking. They are also used in industries such as manufacturing, transportation, energy, and logistics.
What are the benefits of using industrial PCs?
The benefits of using industrial PCs include reliability in harsh environments, long-term availability, compatibility with industrial equipment and protocols, and the ability to withstand extreme conditions. They also offer flexibility in terms of customization and expansion options.
What are the different types of industrial PCs?
There are several types of industrial PCs, including panel PCs, rackmount PCs, box PCs, and embedded PCs. Each type is designed for specific applications and environments, and may have different form factors and features.